切削加工基板
2024.09.15
最初の頃(2007年~)は、自分で購入したCNCを使い切削基板を作っていた。オリジナルマインド COBRA2520
その前に勤めていた会社でCNCを買って、それ以前から切削基板は主に社内で活用していたのだが、とくに試作で同じものを何台も作るときには非常に助かっていた。
ユニバーサル基板で同じものを何台も、というのは本当に勘弁してほしかった。面倒くささマックス。
基本的に片面ながら、パターンが配線されていれば手間暇が全然違う。ずいぶんラクになったし、配線もスッキリした。
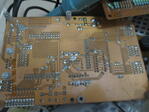
それこそ色んなものを数え切れないぐらい作った。
ただ、パターン同士の隙間に削りカスが挟まっていたり、ハンダ付けをうまくやらないとショートしやすい欠点はあった。そこで顕微鏡で見ながら削りカスを除去するなどの手間はかかっていた。
銅箔の研磨も兼ねて、スコッチブライトやスチールウールで擦っていたけど、その時に削りカスもある程度は落ちる。完全には落としきれない。
パターンを引くのはどうしたかというと、これはもう完全に手作業で、最初の頃は基板設計CADをうまく使えなかったから、
フリーソフトの2次元のCADを使い、2.54mmピッチあるいは1.27mmといったグリッドに補助線でパターンを描いていき(配線済みの線は紙の回路図の塗りつぶしを行う)、
パターンの太さに合わせて、たとえば0.3mmだったらオフセット0.15として両サイドに膨らませ、最終的にパターンの断片同士をつなぎ合わせる編集を行っていた。
何のことやらわけがわからんだろうな。
基本的に片面パターンで済むように、最低限のジャンパー線で済むように、部品配置や配線の仕方、回路の見直しまで行いながら進めていた。
ガーバーデータから輪郭線を抽出すれば・・・というのは分かっていたが、いまいちうまくできなかったのか、忘れたけれど結局やらなかった。
それでさっきのCADからDXF出力し、CAMソフトを使って、パターンデータ、穴あけデータ、外形データの3つに分けて出力し、CNCへ持っていって加工していた。
MITSかLPKFの基板切削加工機も検討していて、一番安くて80万ぐらいだったけど、一時期マジで買おうと思って(躊躇する金額だったが)メーカーに電話してやりとりをしたこともある。
でも、その当時でも基板を安価に作れる所は使っていたから、そっちを利用する方が手間や自分の時間はかからないので、結局その機械は買わなかった。
実際の加工に戻るが、
まずパターンを削り出し、
次に穴あけを行って、(刃物を交換)
最後に外形の切り出しを行う(やはり刃物を交換)。
自動的にツールチェンジしてくれる仕組みがあったらいいなあ、と思いながらやっていた。
材料投入から完成品まで、洗濯機みたいに洗濯物と洗剤を放り込んでボタンを押せば、あとは洗濯が終わるのを待つだけ、みたいなのが理想だった。
銅箔を研磨した後、フラックスを塗る。これは銅箔の酸化を抑えるためとハンダ付けしやすくするため。
レジストはできないか。よくある緑色の被膜。これは一時サンハヤトのスプレーを検討したが、選択的にできない、つまりハンダ付けする部分にも付着するため、使えないなあ、と。
ハンダ付けする部分に付着したレジストをいちいち削ってからハンダ付けするのは面倒すぎる。
ハンダ付けする部分を隠すようなマスクが作れたら、と考えたけれど難しい。ポジとネガの関係というか、板に穴あけをして塗装用のマスクを作ろうとしても、隠したい部分は・・・
説明が難しい。
隠したい部分は部品の取付穴など点在していて、板に穴あけのマスクは作りにくい。プリント基板の製造工程では確か写真法で、レジストをかけない(除去したい)所を露光するようなマスクだったと思うけど、
レジストを残したい部分は光を当てないようになっている。
その前に勤めていた会社でCNCを買って、それ以前から切削基板は主に社内で活用していたのだが、とくに試作で同じものを何台も作るときには非常に助かっていた。
ユニバーサル基板で同じものを何台も、というのは本当に勘弁してほしかった。面倒くささマックス。
基本的に片面ながら、パターンが配線されていれば手間暇が全然違う。ずいぶんラクになったし、配線もスッキリした。
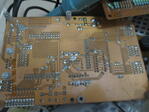
それこそ色んなものを数え切れないぐらい作った。
ただ、パターン同士の隙間に削りカスが挟まっていたり、ハンダ付けをうまくやらないとショートしやすい欠点はあった。そこで顕微鏡で見ながら削りカスを除去するなどの手間はかかっていた。
銅箔の研磨も兼ねて、スコッチブライトやスチールウールで擦っていたけど、その時に削りカスもある程度は落ちる。完全には落としきれない。
パターンを引くのはどうしたかというと、これはもう完全に手作業で、最初の頃は基板設計CADをうまく使えなかったから、
フリーソフトの2次元のCADを使い、2.54mmピッチあるいは1.27mmといったグリッドに補助線でパターンを描いていき(配線済みの線は紙の回路図の塗りつぶしを行う)、
パターンの太さに合わせて、たとえば0.3mmだったらオフセット0.15として両サイドに膨らませ、最終的にパターンの断片同士をつなぎ合わせる編集を行っていた。
何のことやらわけがわからんだろうな。
基本的に片面パターンで済むように、最低限のジャンパー線で済むように、部品配置や配線の仕方、回路の見直しまで行いながら進めていた。
ガーバーデータから輪郭線を抽出すれば・・・というのは分かっていたが、いまいちうまくできなかったのか、忘れたけれど結局やらなかった。
それでさっきのCADからDXF出力し、CAMソフトを使って、パターンデータ、穴あけデータ、外形データの3つに分けて出力し、CNCへ持っていって加工していた。
MITSかLPKFの基板切削加工機も検討していて、一番安くて80万ぐらいだったけど、一時期マジで買おうと思って(躊躇する金額だったが)メーカーに電話してやりとりをしたこともある。
でも、その当時でも基板を安価に作れる所は使っていたから、そっちを利用する方が手間や自分の時間はかからないので、結局その機械は買わなかった。
実際の加工に戻るが、
まずパターンを削り出し、
次に穴あけを行って、(刃物を交換)
最後に外形の切り出しを行う(やはり刃物を交換)。
自動的にツールチェンジしてくれる仕組みがあったらいいなあ、と思いながらやっていた。
材料投入から完成品まで、洗濯機みたいに洗濯物と洗剤を放り込んでボタンを押せば、あとは洗濯が終わるのを待つだけ、みたいなのが理想だった。
銅箔を研磨した後、フラックスを塗る。これは銅箔の酸化を抑えるためとハンダ付けしやすくするため。
レジストはできないか。よくある緑色の被膜。これは一時サンハヤトのスプレーを検討したが、選択的にできない、つまりハンダ付けする部分にも付着するため、使えないなあ、と。
ハンダ付けする部分に付着したレジストをいちいち削ってからハンダ付けするのは面倒すぎる。
ハンダ付けする部分を隠すようなマスクが作れたら、と考えたけれど難しい。ポジとネガの関係というか、板に穴あけをして塗装用のマスクを作ろうとしても、隠したい部分は・・・
説明が難しい。
隠したい部分は部品の取付穴など点在していて、板に穴あけのマスクは作りにくい。プリント基板の製造工程では確か写真法で、レジストをかけない(除去したい)所を露光するようなマスクだったと思うけど、
レジストを残したい部分は光を当てないようになっている。